D’Apt à Gargas, le dernier ocrier d’Europe
a repris des couleurs
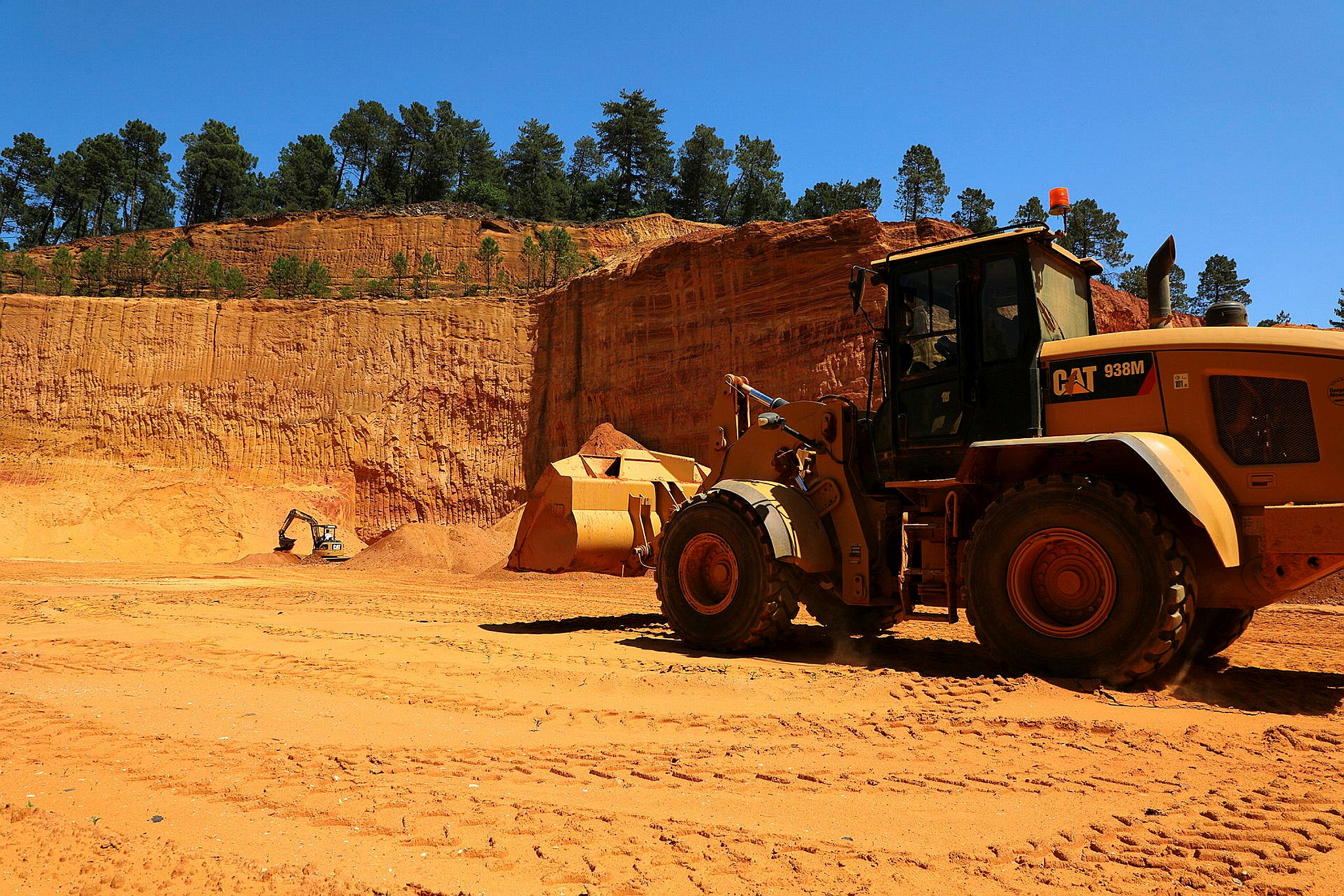
Les Ocres de Provence
perpétuent dans le Vaucluse
un savoir-faire historique :
la transformation du minerai vauclusien
en pigment, utilisé en décoration notamment
Amusant paradoxe : en l’état actuel des choses, l’ocre provençal est privé d’IGP. Pourquoi ? Parce qu’il faut un consortium
de producteurs pour établir le cahier des charges d’une indication géographique protégée. Et que cette industrie séculaire
ne compte plus… qu’un seul producteur dans toute
l’Europe : la Société des ocres de France. Avec sa carrière à Gargas et son usine à Apt, l’entreprise familiale - plus connue
sous la marque "Ocres de France" - est l’héritière d’un savoir-faire rare et méconnu : la production de pigments, à partir
de ces falaises dont la silhouette orange flamboyante se découpe sur le ciel d’un bleu intense du début d’été.
Depuis sa création, en 1901, le processus n’a pas bougé : extraction du minerai en carrière, séparation de l’ocre et du sable, lavage, séchage en plein air, puis broyage, cuisson parfois, conditionnement et vente. Historiquement, le premier marché
de l’ocre, est celui des professionnels du BTP et de la décoration. Au fil des ans, pourtant, portée par la vague du retour au naturel et des circuits courts, accélérée par des ouvertures stratégiques successives - vers le B2C, vers des marchés, vers l’international - la société su pérenniser leur activité. Son logo - un coq surmontant deux globes terrestres, qui n’a pas changé
depuis 1901 - raconte un peu de cette fierté française d’avoir su conserver le savoir-faire vauclusien. Visite guidée.
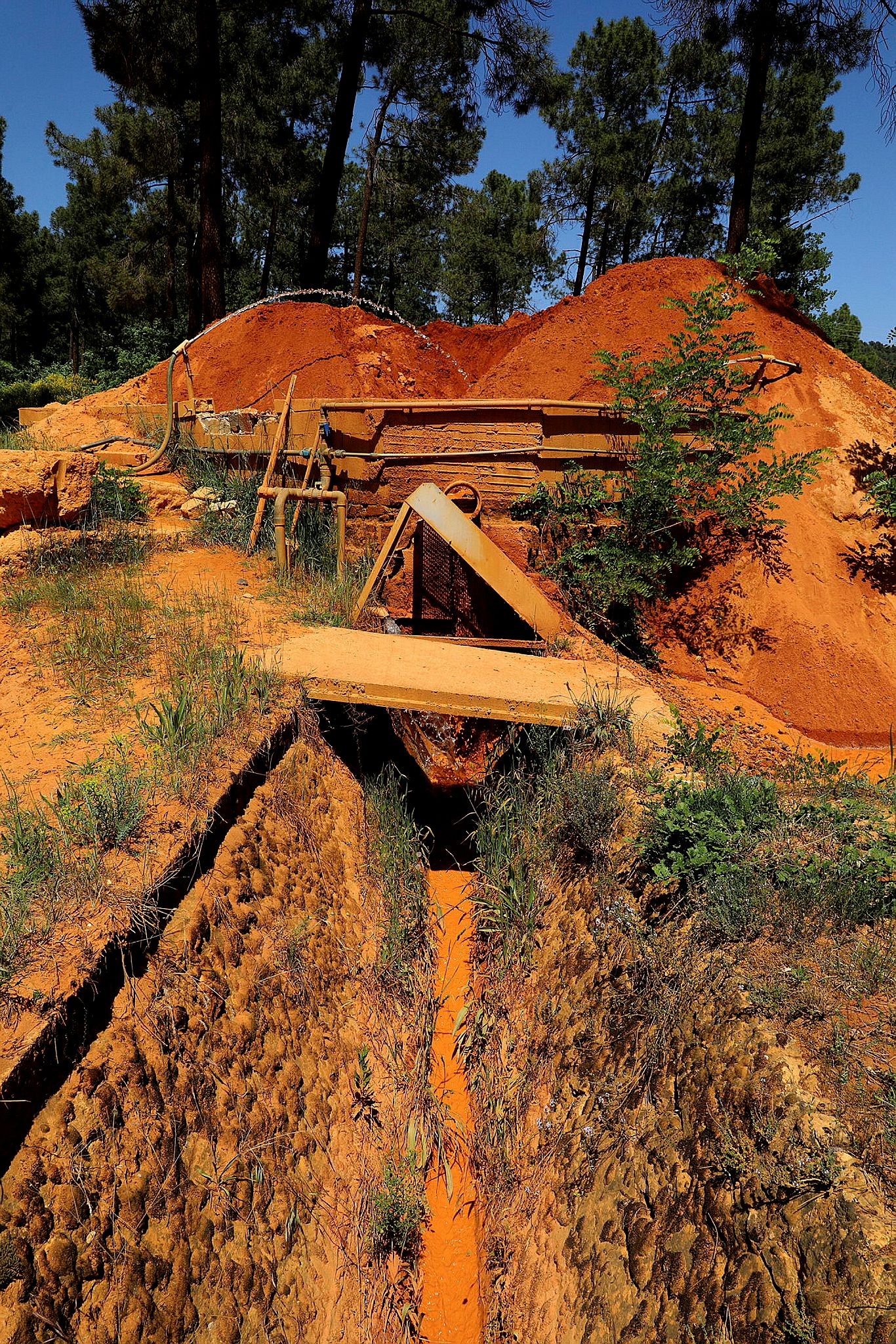
Dans la station de lavage, le minerai, entraîné par l'eau, passe à travers un séparateur grâce à la force centrifuge. L'ocre est récupérée, le sable rejeté / Valérie SUAU
Dans la station de lavage, le minerai, entraîné par l'eau, passe à travers un séparateur grâce à la force centrifuge. L'ocre est récupérée, le sable rejeté / Valérie SUAU
Un savoir-faire ancestral, remis au goût du jour
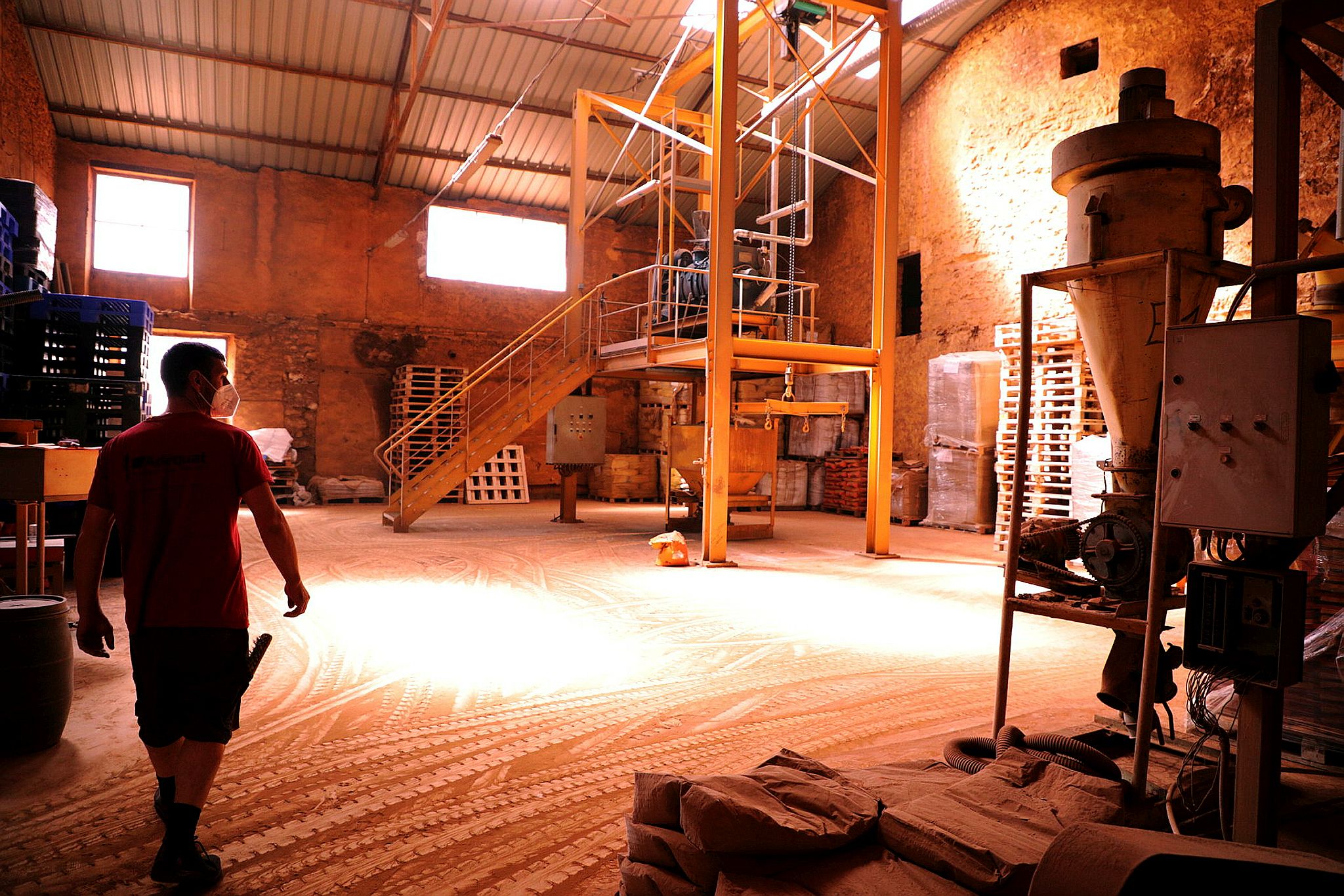
Dans le Vaucluse, les Ocres de France extraient 800 à 1 000 tonnes par an de cet or jaune recherché
Curieusement, c’est parfois à la barre d’un tribunal de commerce, au bord de la liquidation, que commencent les belles histoires.
En 1974, la Société des ocres de France, en faillite, a failli disparaître. C’était sans compter l’opiniâtreté d’un maçon aptésien, Gilbert Guigou. C’est à lui - et à ses descendants -
que l’on doit de conserver dans le Vaucluse le dernier ocrier
de France, et même d’Europe. L’entreprise gère la dernière carrière en activité, à Gargas, et transforme l’ocre extraite
dans son usine d’Apt.
En cet après-midi du milieu du mois de mai, dans la fameuse carrière, une petite pelleteuse et un transporteur s’activent.
C’est la fin de la période d’extraction ; elle a duré 15 jours.
Pour accéder à l’endroit, il a fallu dépasser le panneau "entrée réglementée" qui barre le chemin. Sur le sol, du sable fin couleur rouille recouvre le tapis forestier. Contrairement à certaines parties du massif des ocres, qui accueillent les touristes, ce terrain de 20 hectares est privé et c’est un site industriel. "La grande pelle a déjà fait tomber tout ce que nous voulions extraire, désormais
la petite termine le tri, et le transporteur emmène le chargement jusqu’à la station de lavage, explique Stéphanie Anglès-Guigou, co-directrice générale de la Société des ocres de France.
Du minerai de la carrière, qui est formé de 20% environ d’oxyde de fer, et de kaolin avec du sable siliceux, on extrait environ 10% d’ocre." Quand elle était petite, la falaise qui se dresse à pic, à une bonne vingtaine de mètres de hauteur, était plus proche. Elle a reculé
un peu au fil des années. "Nous dépendons d’autorisations d’extraire qui sont délivrées par le ministère de l’Écologie,
reprend-elle, nous avons le droit d’extraire de quoi produire l’équivalent de 800 à 1 000 tonnes d’ocre par an."
"C’est la dernière carrière d’ocre d’Europe. Le site
a besoin de surveillance, car les gens viennent
par curiosité touristique quand il est fermé. D’autant que sous nos pieds, il y a les galeries
des anciennes mines."
Quelques centaines de mètres plus loin, la station de lavage historique se déploie en plein air. Elle tourne à plein régime,
pour sa dernière année ; à une dizaine de mètres, un bassin
en béton annonce la mise en service prochaine d’une station
de lavage toute neuve. Déposé en tas par le chargeur piloté
par Pierre, l’un des salariés, le sable coloré part sous la pression d’un jet d’eau dans un bassin en pierre, puis au travers
d’un batardeau, une petite digue. 300 m³ d’eau sont nécessaires chaque jour, puisés dans une source souterraine. Mais le cycle,
en circuit fermé, permet de limiter fortement la déperdition d’or bleu. Dans le pays de l’ocre, on craint la sécheresse.
Liquide, la matière est propulsée à travers un séparateur,
qui grâce à la force centrifuge, sépare le sable de l’ocre.
Le premier est rejeté - il sera ensuite revendu à des acteurs du BTP, pour faire du remblai… L’ocre, elle, se faufile dans les tuyaux cachés dans les collines jusqu’aux bassins de décantation.
Les Ocres de France en exploitent cinq, deux autres sont
en construction. L’ocre y est déposée, l’eau est récupérée.
Un passage sur une zone de séchage pendant quelques semaines achève le processus.
Ensuite, direction l’usine, car c’est à Apt que se poursuit la route de l’ocre. Un site de production étonnant, où l’ancien voisine avec le moderne. Des bâtiments vieux et nouveaux se mêlent,
les pierres sèches sont accolées aux parpaings, les tuiles traditionnelles aux toits de tôle. La poussière d’ocre recouvre tout, jusqu’à la trottinette électrique laissée à l’entrée
d’un hangar. Sous un auvent gigantesque, des cases où sont stockées les ocres en attente d’être traitées. Dans le bâtiment mitoyen, une broyeuse tourne à plein régime ; elle réduit
la matière en poussière de 10 à 30 microns d’épaisseur.
Dans un rai de lumière qui traverse la pièce à la charpente apparente, les particules en suspension semblent danser.
Plus loin, des mélangeurs créent différentes teintes de pigments : "Par exemple, de l’ocre jaune avec de la phtalocyanine de cuivre bleue permettent d’obtenir du pigment vert", illustre la maîtresse
des lieux. À l’extrémité du bâtiment, sous un auvent, un four flambant neuf. Il permet de produire ce fameux ocre rouge ;
15 minutes à 750ºC permettant de déshydrater l’oxyde de fer,
lui donnant cette couleur couleur brique si particulière.
La fin de la production, elle, est plus classique : lignes
de conditionnement, en sacs ou en flacons, puis stockage. Entre
la falaise et les étagères de vente, un an en moyenne se sera écoulé. Le temps nécessaire à l’accomplissement d’un processus qui n’a presque pas changé depuis plus d’un siècle.
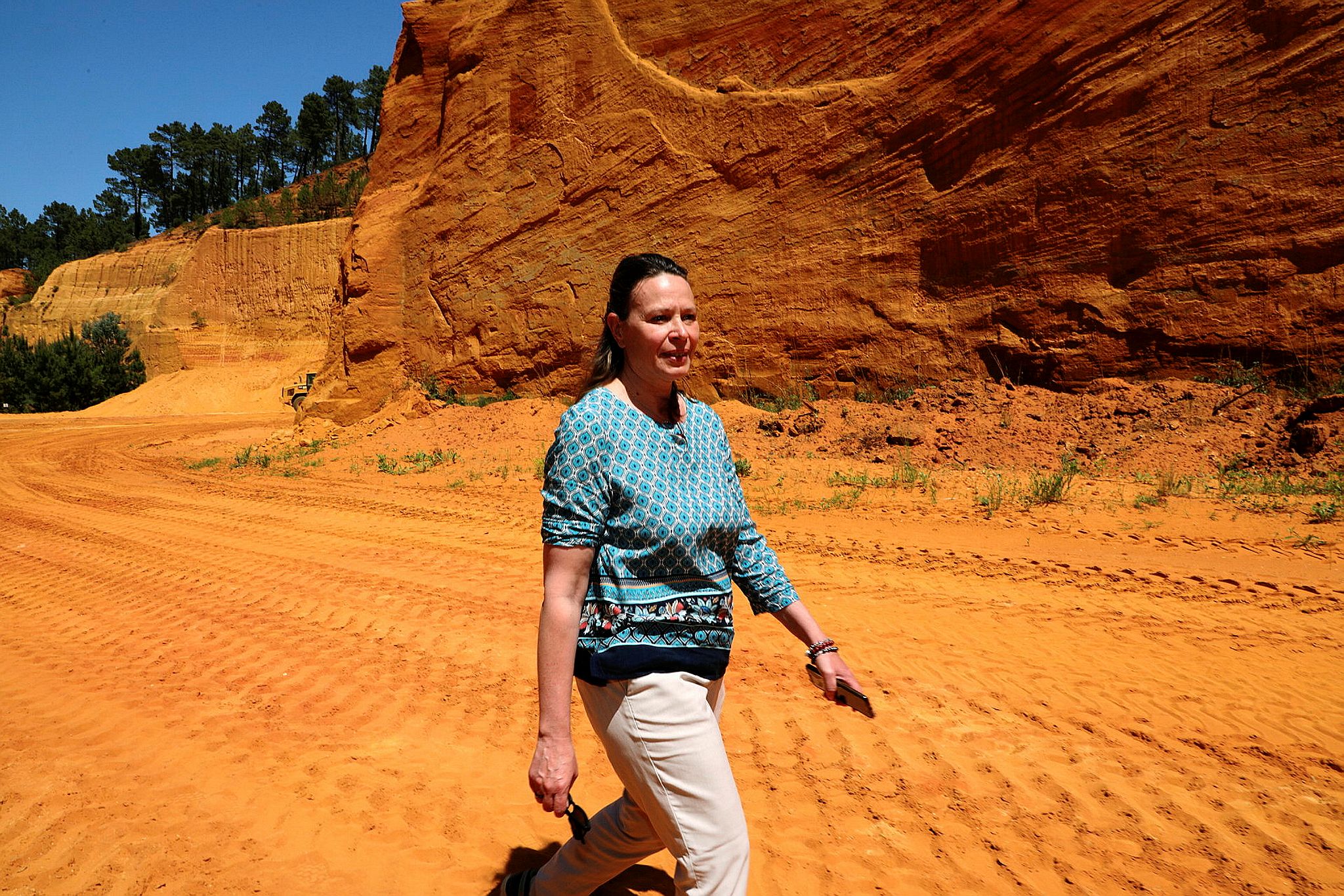
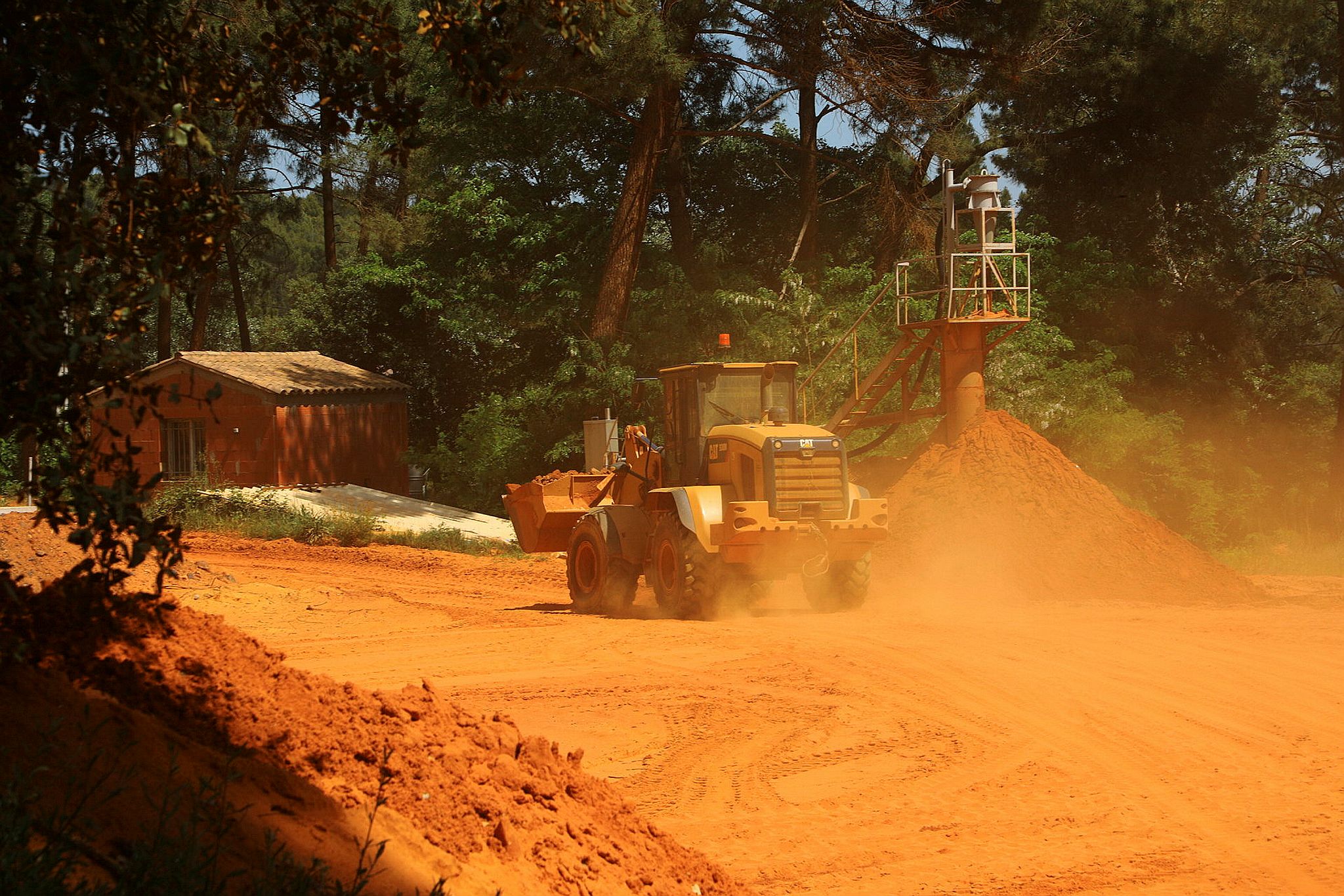
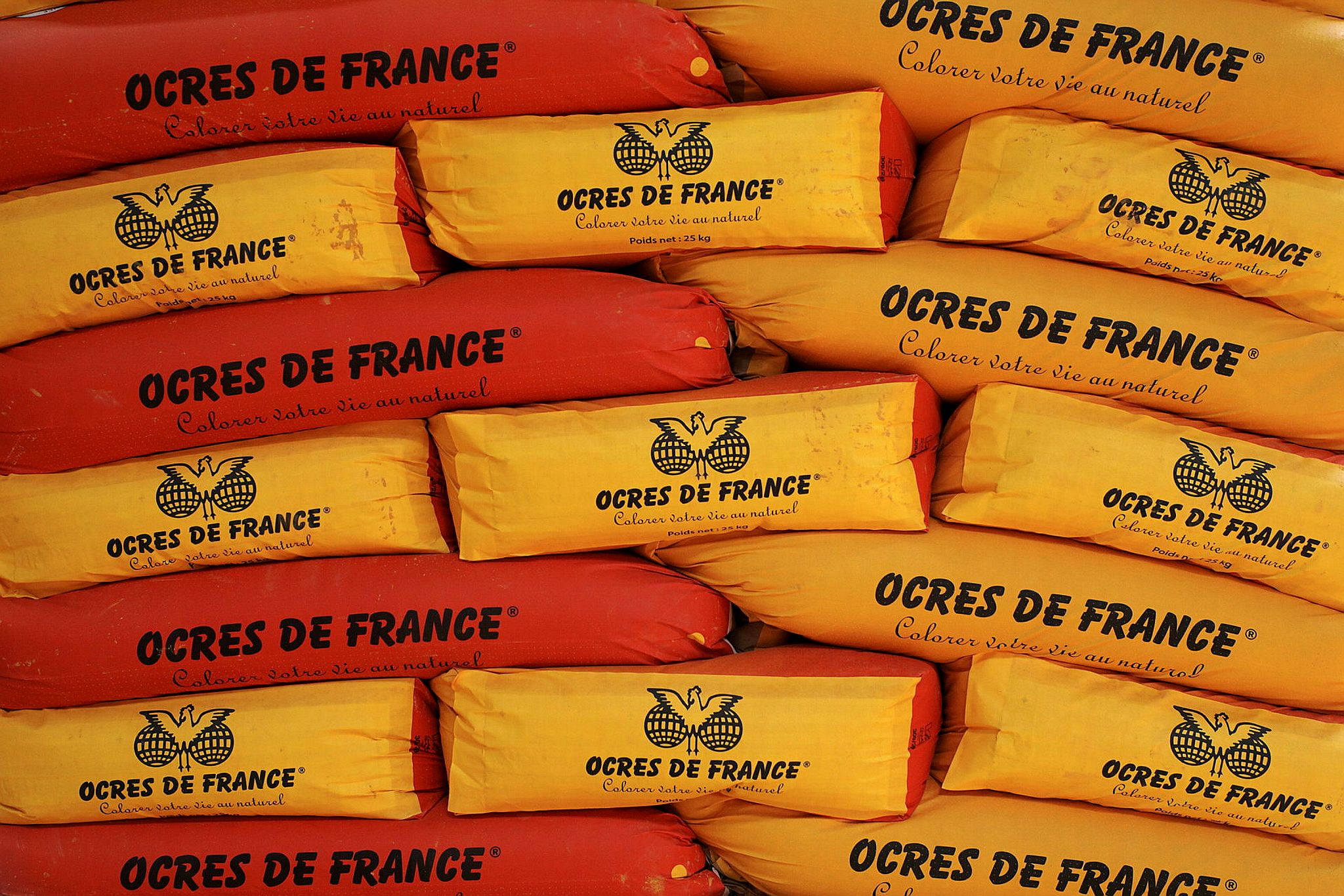
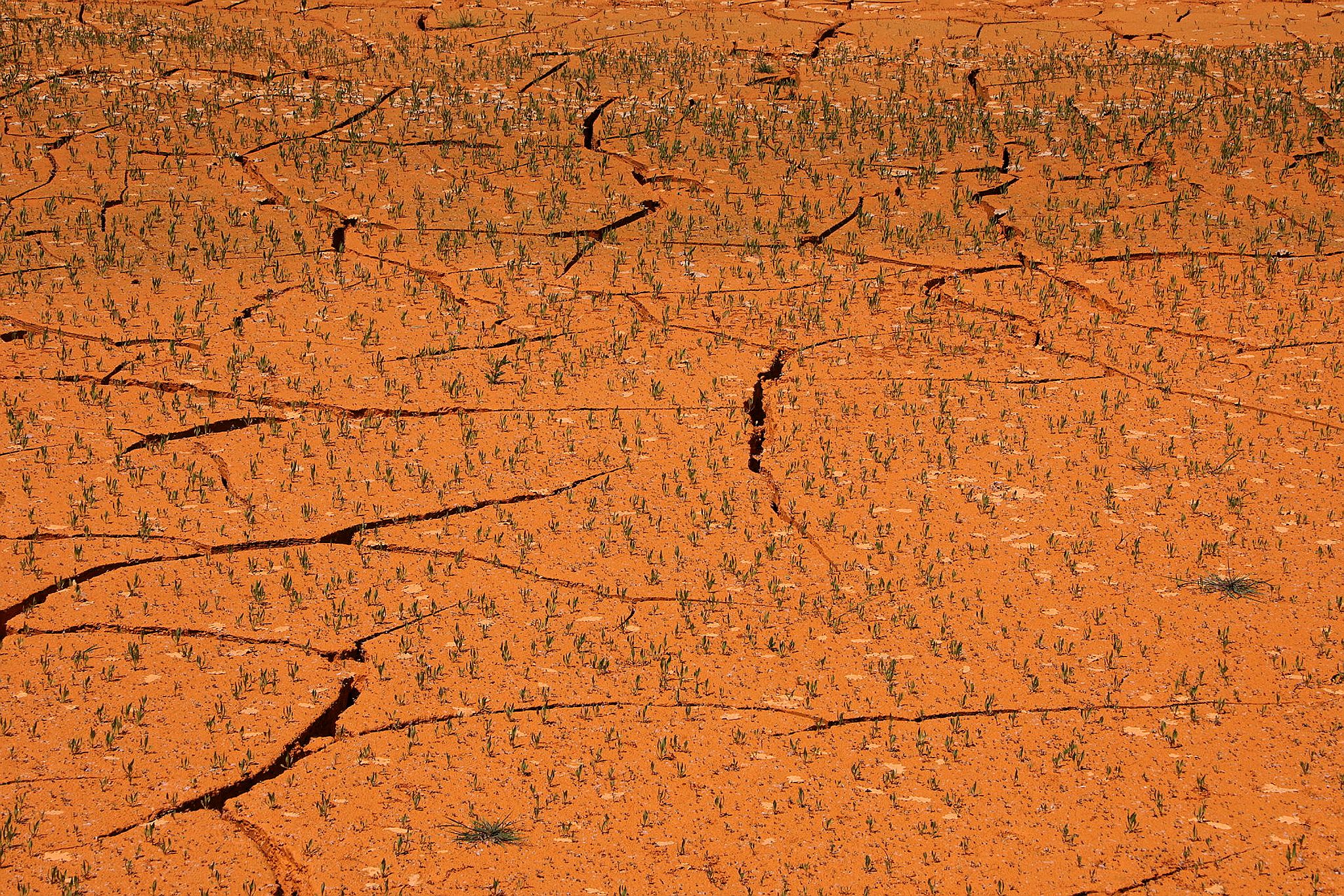
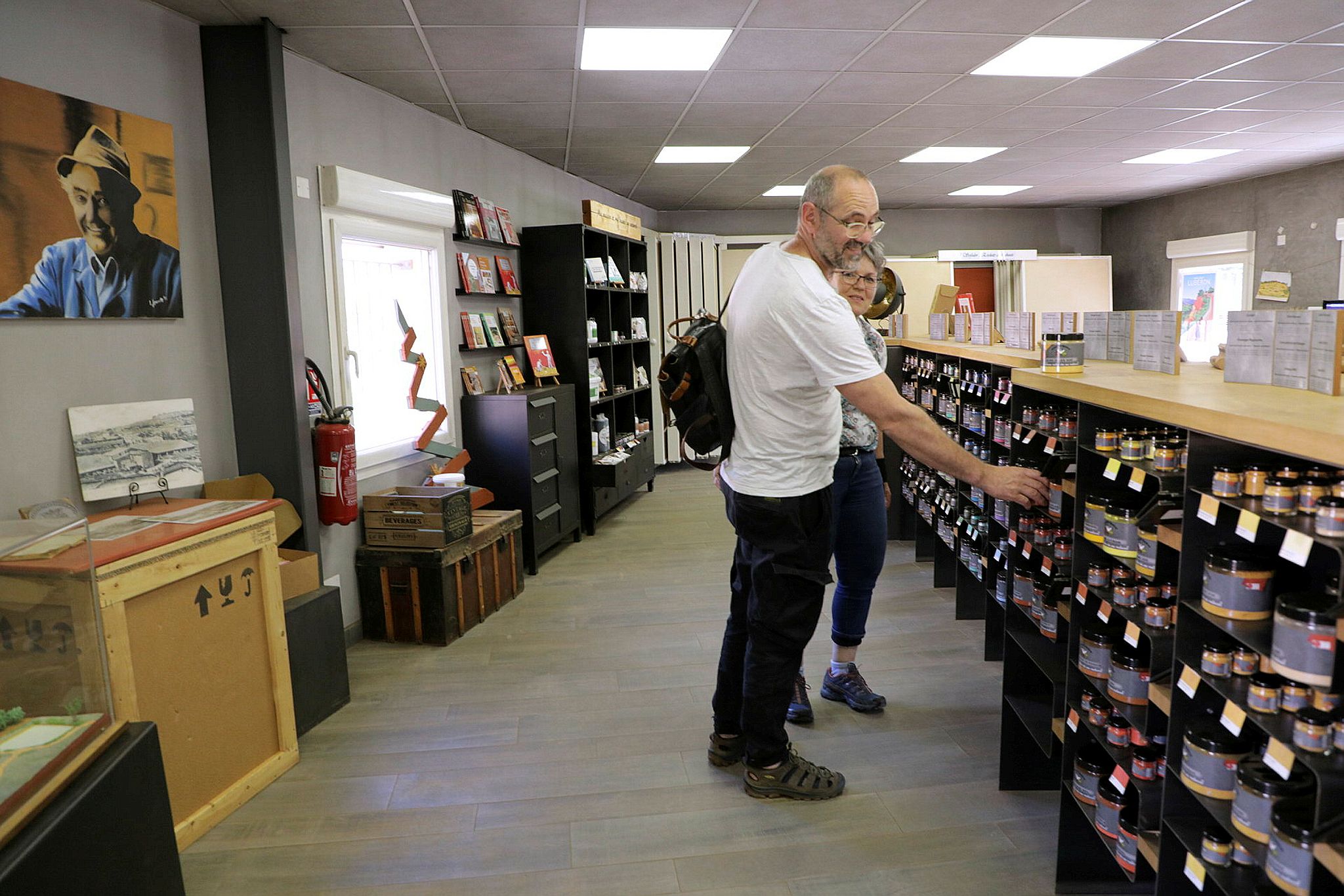
Depuis 2015, la société familiale a créé un petit showroom dans son usine d’Apt / Valérie SUAU
Depuis 2015, la société familiale a créé un petit showroom dans son usine d’Apt / Valérie SUAU
La stratégie :
les ocres à la conquête de nouveaux marchés
Comme souvent dans les entreprises, la longévité de la Société des ocres de France tient beaucoup à la diversification progressive de ses activités. "Mon grand-père, qui était un amoureux de l’ocre, un enfant du pays a racheté l’entreprise, car il ne se voyait pas
la laisser sombrer, se remémore Stéphanie Anglès-Guigou.
Au début, il a eu peu de clients mais ça lui a permis de faire
des travaux. Puis quelques jolis contrats l’ont fait tourner. En 1985, mon père et mon oncle sont arrivés dans l’entreprise et ont pris
la suite. Ils ont diversifié les conditionnements, les couleurs,
les chaux… Et puis en 2000, la société a énormément profité
de la vague du retour au naturel, un vrai boost."
Le marché historique de l’ocre, le bâtiment et la décoration, est resté le socle de la société, qui aujourd’hui encore, réalise
une grande part de son activité en B2B. L’entreprise commercialise à présent une centaine de pigments - certains étant le fruit de mélanges avec d’autres couleurs venues
de l’extérieur - mais aussi 46 badigeons et 24 enduits de façade. Elle a notamment collaboré il y a quelques années avec Lafarge, pour mettre au point une gamme de plâtres.
À ce marché principal, sont aussi venues se greffer des niches :
en premier lieu, celui de la cosmétique, pour lequel chaque année, une partie de l’ocre extraite à Gargas est analysée (pour s’assurer de l’absence de métaux lourds), labellisée Cosmécert et vendue
à des sociétés comme Aromazone. "Nous vendons aussi au marché du savon, et depuis quelques années, au secteur événementiel, pour les fêtes comme les color-run, dans lesquelles les gens s’envoient
des pigments colorés", ajoute la directrice générale.
Mais au fil des années, et c’est sans doute la partie la plus inattendue du business model, les Ocres de France se sont aussi tournés vers l’international, qui représente aujourd’hui 60%
de l’activité. En Europe, mais aussi et surtout en Afrique,
où le pigment connaît un succès fracassant depuis trois ans, sans que les producteurs vauclusiens ne puissent en identifier
la raison. "Nous expédiions deux ou trois conteneurs par an
à l’étranger jusqu’en 2019, aujourd’hui, ce sont 70 conteneurs !", constate Stéphanie Anglès-Guigou. Un appel d’air bienvenu,
qui en compensant la perte de certains autres clients, a permis
à l’entreprise de garder sa stabilité et envisager de nouveaux investissements.
Plan d’investissements :
renouveler l’outil industriel pour produire plus
C’est le gros chantier qui occupe les dirigeants de la Société
des ocres de France actuellement : le renouvellement des outils de production. En janvier dernier, un nouveau four est entré
en activité ; il a nécessité trois ans d’installation, et est venu remplacer son antique prédécesseur, véritable "pièce de musée", chauffant au gaz l’ocre à 750ºC. "Grâce à lui, nous allons obtenir des ocres différentes avec des températures et des temps de cuisson différents, des tests sont prévus", précise Stéphanie Anglès-Guigou.
En parallèle, l’entreprise a aussi lancé de gros investissements, dans la station de lavage d’une part, et dans le conditionnement. L’antique station de lavage, qui tourne toujours, sera ainsi remplacée d’ici le printemps prochain, pour entrer en fonction
à la prochaine extraction. Loin d’être anecdotique, la nouvelle station devrait permettre d’extraire plus de pigment du minerai. Autrement dit, de produire plus sans extraire plus des collines, puisqu’un arrêté ministériel restreint fermement les volumes prélevés sur la falaise. Investissement consenti : 100 000 €.
The last but not the least, la nouvelle emballeuse des Ocres
de France, pour un coût de 220 000€, a fait l’objet
d’une subvention régionale ; la collectivité en a pris en charge près de la moitié.
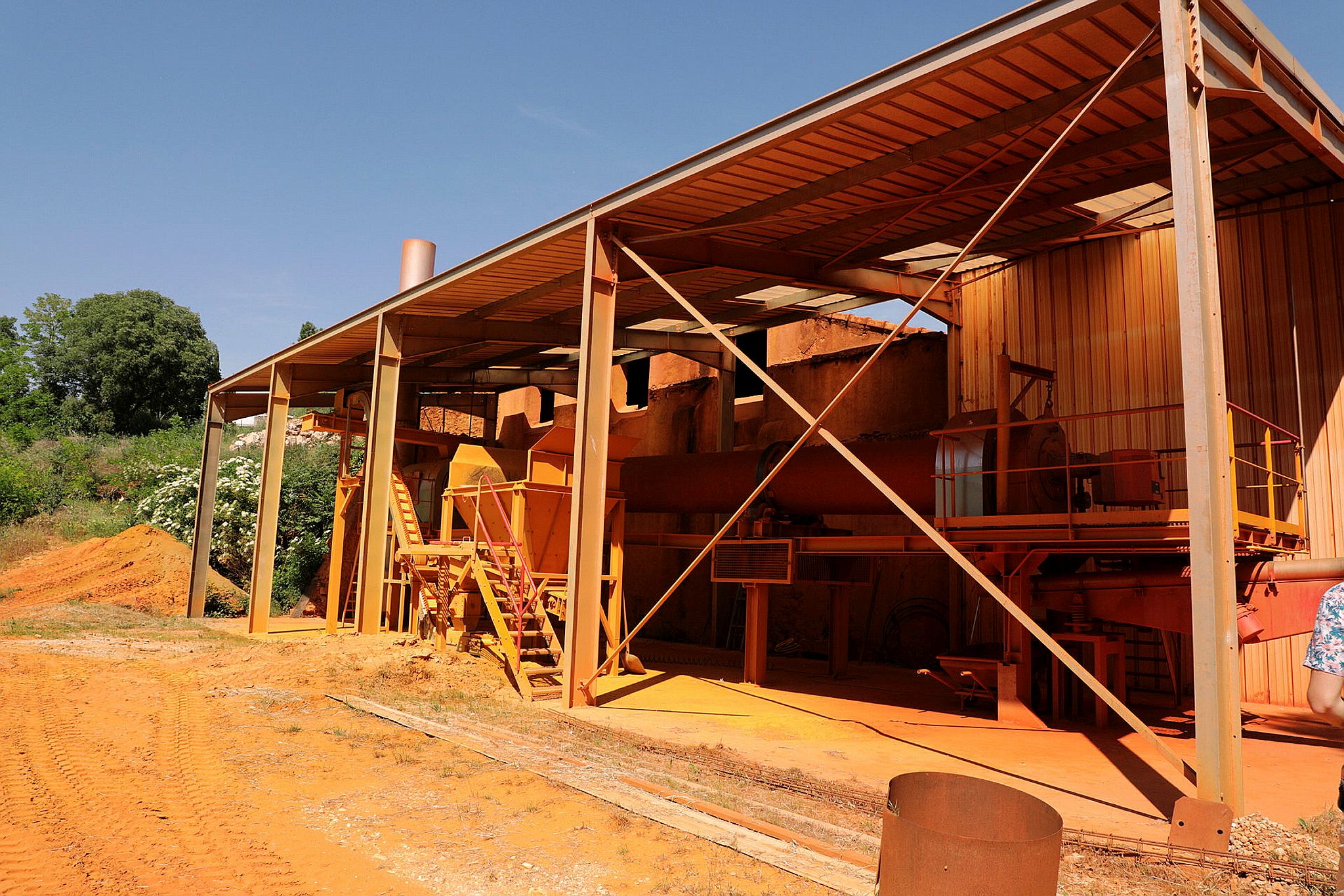
Le nouveau four, entré en fonction en janvier 2021, permet de produire l’ocre rouge, qui cuit 15 minutes à 750°C / Valérie SUAU
Le nouveau four, entré en fonction en janvier 2021, permet de produire l’ocre rouge, qui cuit 15 minutes à 750°C / Valérie SUAU
/ Thierry SABATON
/ Thierry SABATON
En chiffres
- 1901 : la date de création de la Société des ocres de France. Elle est reprise en 1974, alors en faillite, par Gilbert Guigou
- 4 générations se sont succédé depuis le maçon aptésien. L’entreprise est co-dirigée par la troisième, Brice Guigou
et sa sœur Stéphanie Anglès-Guigou depuis 2016. La fille
de Stéphanie, Ludivine, a rejoint la société en 2020 - 10 salariés permanents travaillent pour les Ocres de France, dont neuf à Apt, sur le site de l’usine et un en carrière
- 2,5 millions d’euros : le chiffre d’affaires pour 2020/21, relativement stable
- 20 hectares : la superficie du terrain - privé - où sont installées la carrière et la station de lavage à Gargas